ENGINEERING PROJECTS
Hello!
NOTE: Bellow you’ll find a small sample of my engineering projects. Each project showcases a different aspect of my acquired knowledge/skills. I’ve worked on many projects, much of which I can not discuss due to NDA’s. Please view what I can supply below!
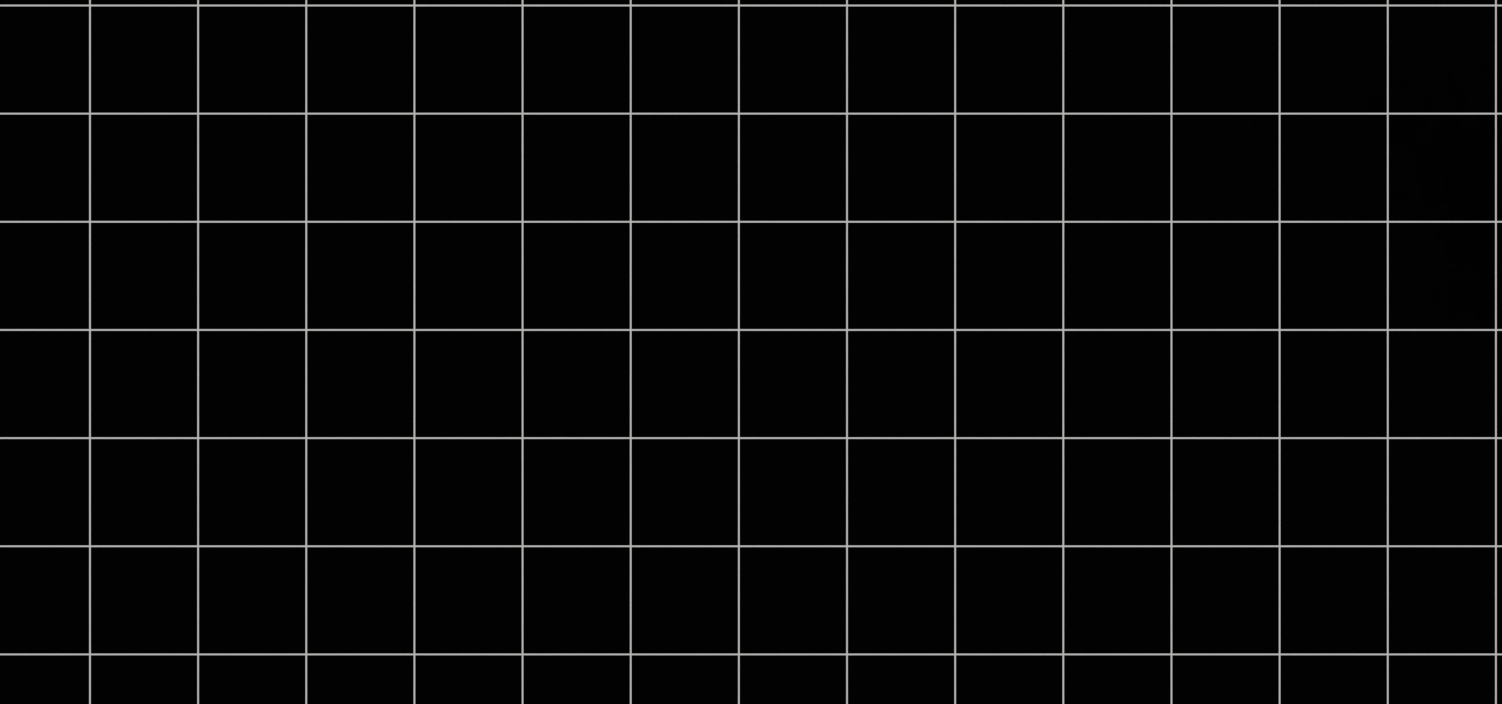
Q.A Machine Rough Draft Animation-Showcase: Engineering knowledge & 3d Design
During a new model build event involving a car seat recliner, a quality assurance check was required to ensure the final good (F.G.) met a rotational torque requirement. Around 500-750k F.G. assembly’s were required each year. After calculating the TAK time and cycle times on all machines in the build. It became apparent hand checking every product would not be remotely possible. Thus a machine was needed built. Due to the importance of the check and time frame of the build an outside contractor was used to alleviate any responsibility’s in error. To Help with the process of the machine design, and to supply our standards, a rough draft of the machine was made. With it an Animation was supplied to showcase our expectations of the cycle. Following this, I lead in discussions in further build meetings and ensured it was designed and built to our standard’s and specifications. The final Design ended up being very close to my initial rough draft.
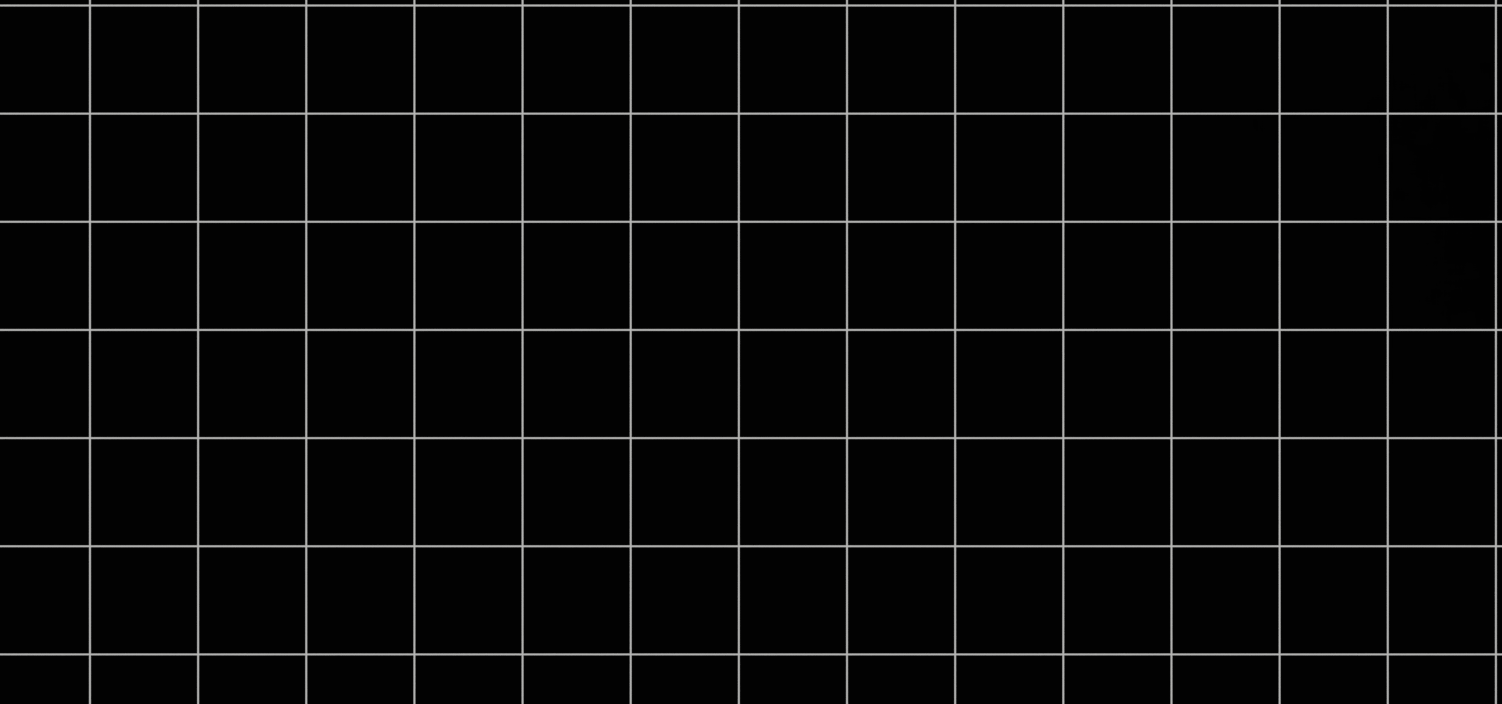
AUTO LOADING, LOCATING & SPATTER SHIELD WELD CELL CLAMP-Showcase: Divergent Thinking, Robotic Mig Welding & Engineering knowledge & 3D DESIGN
this prototypes purpose was to increase efficiency in brkt loading, as well as to shield spatter from assembly. the cup would swivel around and allow operator to load brkt. then would swivel back and be lowered in place via a pneumatic cylinder.
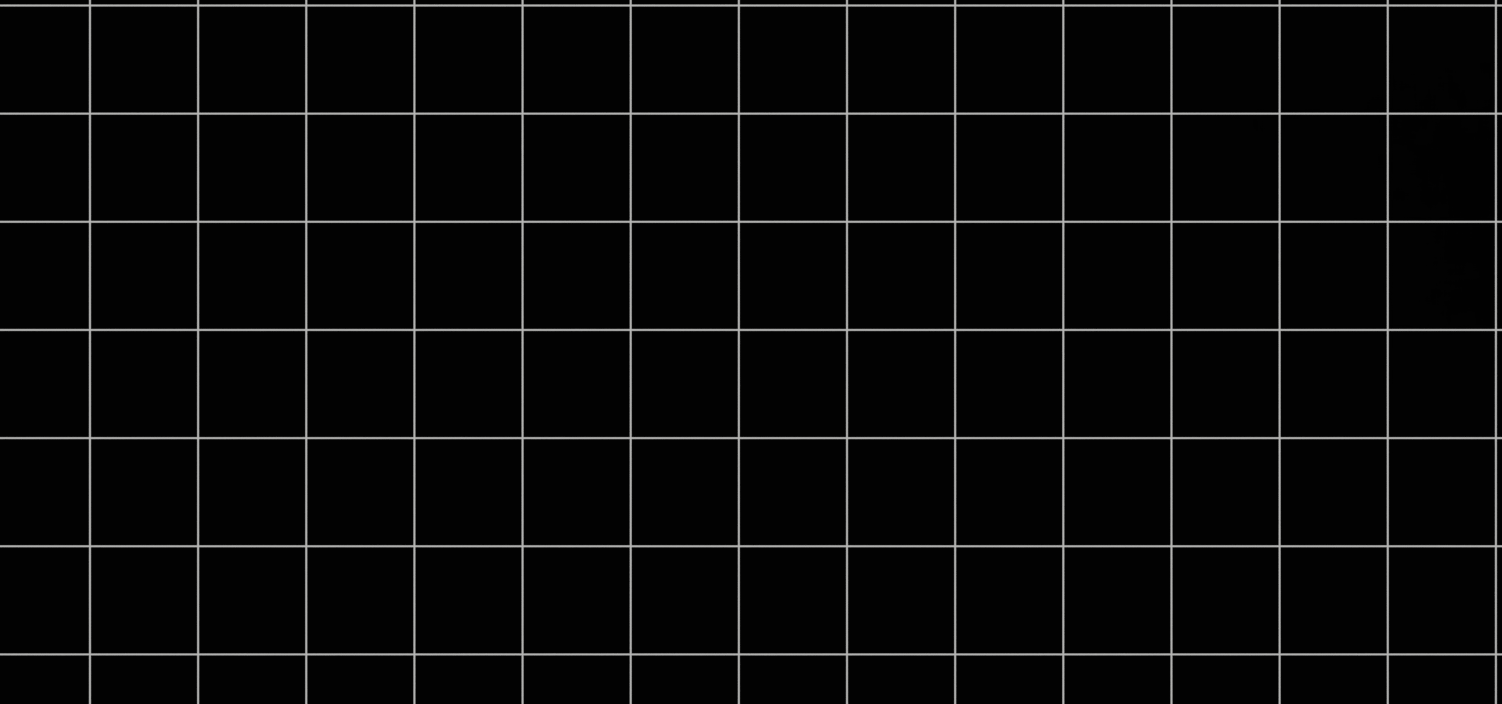
Engr. Thesis: Engineering Design of a 3D-printed Tube Bending Die *Patent Pending-Showcase: Problem solving & FEA
The client approached the team with a problem involving the cost of custom tube bender dies. Due to the company’s ever changing clientele and projects a constant stream of dies were required. Costing anywhere between $500-$2000 and taking several weeks to acquire. My duty’s involved the design and FEA (Finite Element Analysis) of prototypes and the final design. The end product utilized a steel backing created by individual layers of plasma cut steel (Multiple CNC plasma cutters were available to the client). With the outside contour beings 3D printed. This allowed the client to standardize internal backings and would only require 3D printing the outside contour for each new model.
file_open
CLICK THESE LINKS (ABOVE) FOR MORE INFO
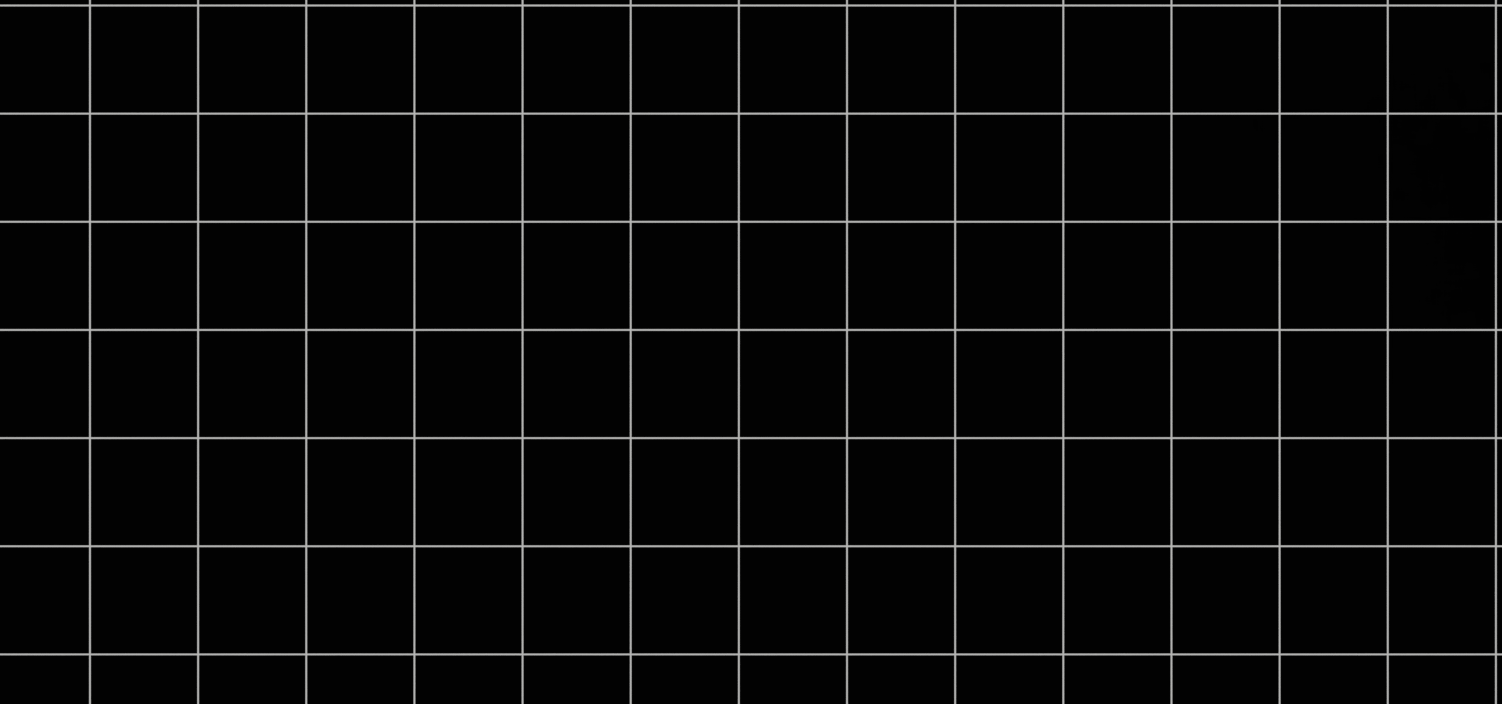
Weld Spatter Study-Showcase: Divergent Thinking, Robotic Mig Welding & Engineering knowledge
A machine was causing excess spatter build on a sub-comp. This caused many issues down the line with every machine causing further error stacking. Also the spatter became a significant waste of MIG Wire and Red Tub Comps/F.G. (recycled sub-assembly’s & F.G. -assembly’s). Furthermore, the machine itself was taking on extra added wear. After months of trial and error from our weld tech. and even outside contractor help. no solutions could be found. I decided to take a different approach and measure the resistance over the full weld cycle. Although The resistance itself can not be deemed accurate due to the presence of voltage and heat. My hypotheses was that, when the data was graphed the curves should be normalized. Because the current in a system is proportional to the voltage flowing. Inversely the resistance is also proportional. The study showed this theory to be true and when compared to the weld sequence itself the weld/welds at fault can be determined. This drastically improves maintenance, as instead of changing the program as a whole and more focused approach can be made.
file_open

Resistance Weld Fixture-Showcase: Mathematical analysis, Resistance Welding, Engineering knowledge & 3D Design
THe previous weld fixture was causing significant error stacking due to propagation. This was due to the old fixture only using one weld nut and requiring the operator to turn the plate for each weld (x4 welds). Each weld nut was only being aligned by the center locator. Even though the clients dwg’s placed a precedence on the importance of the distance between the 4 bushings. First, I calculated the propagation of error of the previous fixture and its weld methodology. I compared the result to the clients specs and saw that a high percentage of F.G. Assembly’s would fail spec. Using my same approach I found the propagation to be significantly less if all 4 bushings were welded in sequence. Thus I designed and had the new weld fixture built. The results showed a massive decrease in fallout.
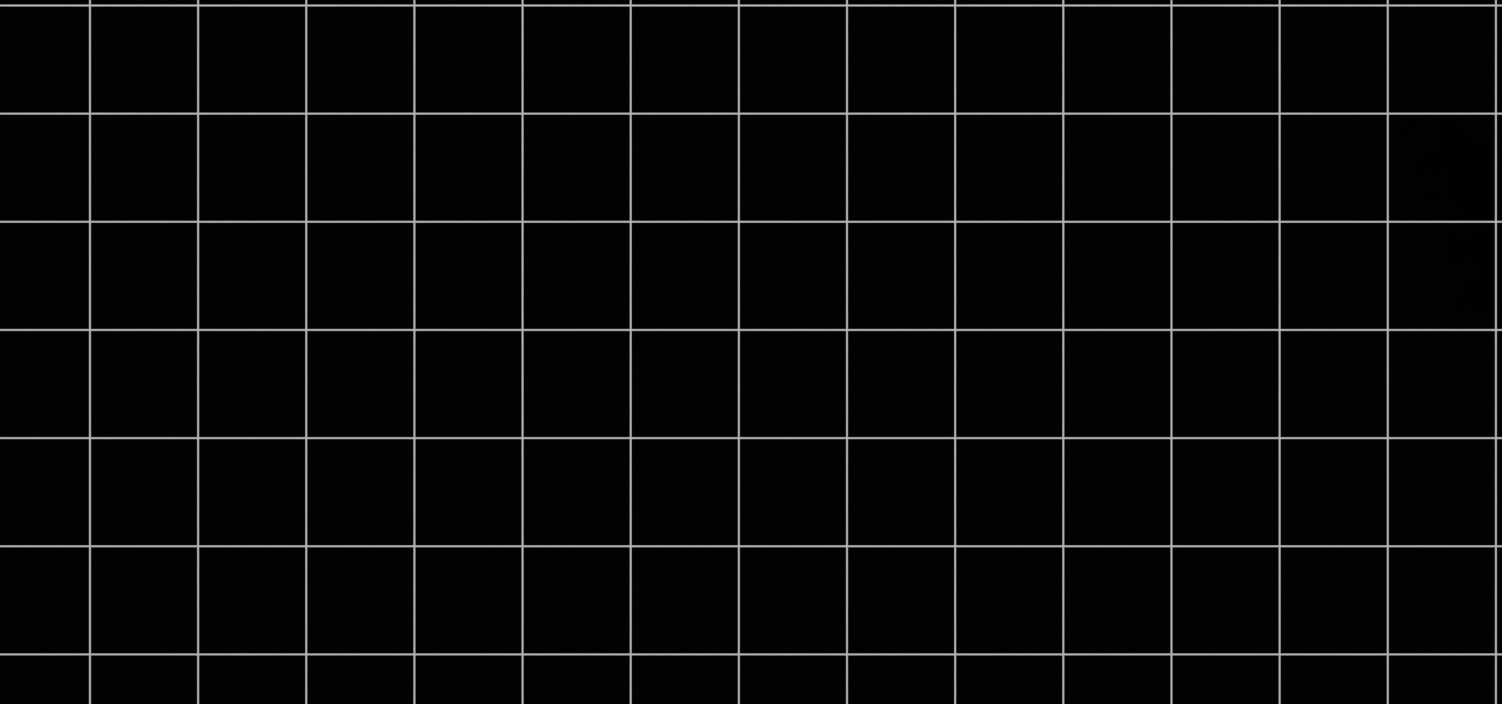
Static analysis of die racks-Showcase: Static analysis, FEA, Layout planning & 3D Design.
I wAs approached with the issue of a lack of available die racks. As well as the fact the none of the racks could hold are 20k+ lb dies. Thus I designed and analyzed the new racks that could support three large dies each. I then also planned out the layout proposal in autodesk. And presented my findings to gain signatures to fund the project. The project was accepted and the layout changeover was made using my layout dwg.
file_open
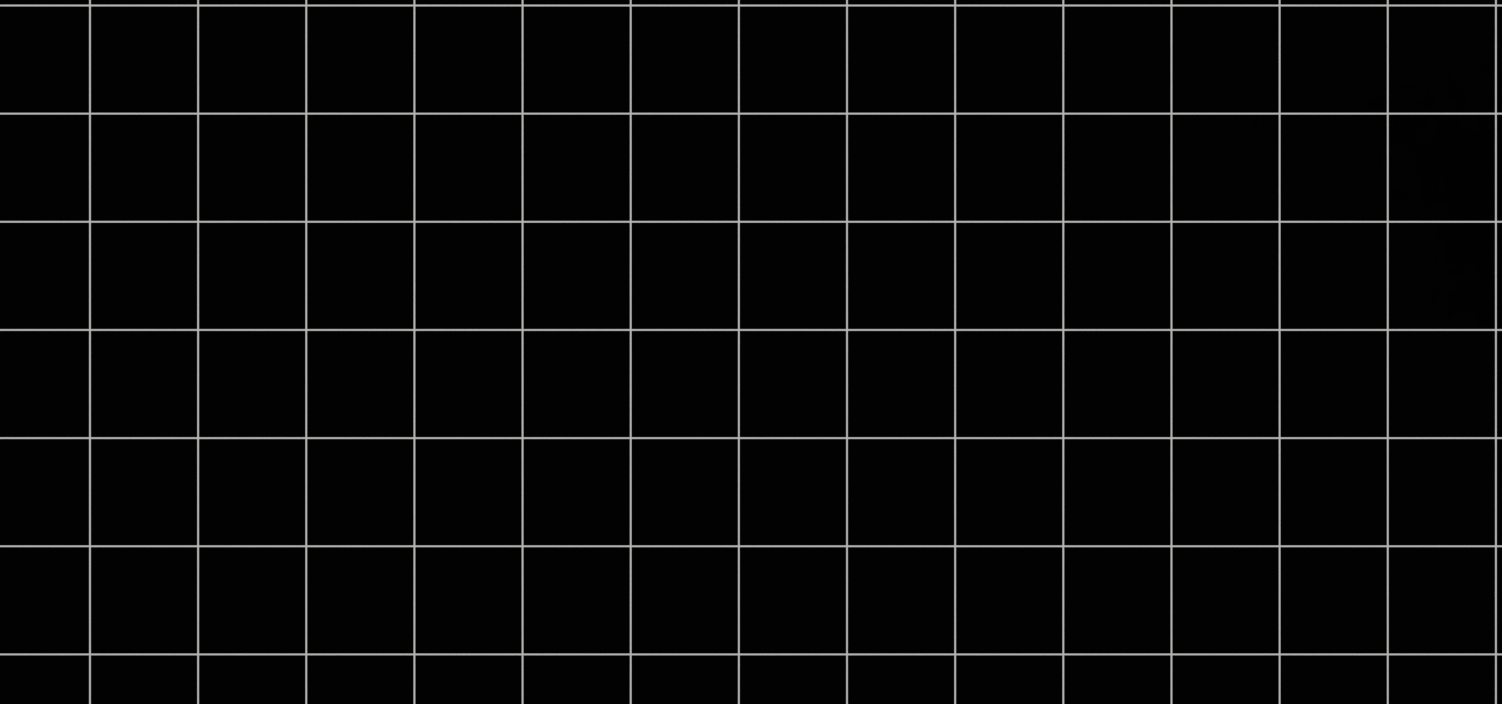
Auto Deburring machine-Showcase: Engineering Knowledge, problem solving & 3D design
Whilst interning at Malco Vice grips, I was placed on a skunk works team in an effort to design and build a improved deburring machine in 6 weeks. I lead in the 3d design of the machine. I designed it such that the operator just loads a ramp with the grips and the machine handles the rest. *Note*-The video shown to the right was during an initial test. I had concluded my internship at this point. following this, proper safety guarding and buttons were added.
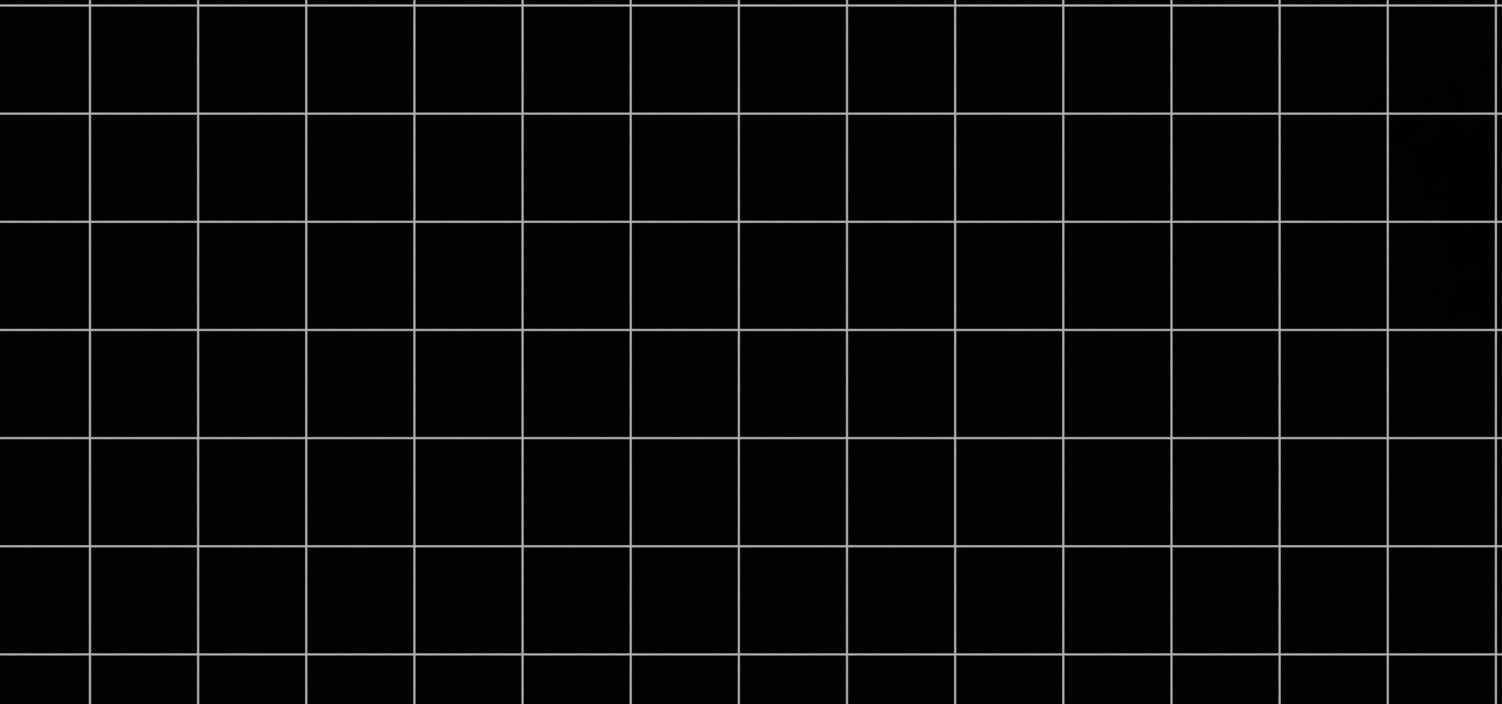
Sensor Unit Improvement-Showcase: Divergent thinking, Engineering knowledge & 3D design
A problem with failing proximity sensors was brought to me. The sensors at times would need changed weekly costing $100-$300 each. After the weld tech failed to find a solution. I decided to try utilizing a misfeed sensor unit. This sensor is commonly used in dies. But I theorized it would work well for our application, as the sensor could be moved away from the welding zone and completely covered. meanwhile the pin itself would protrude from a small hole to sense a bracket that was already being shielded. The pins themselves only cost $10-20$. After a successful initial run of several month on one fixture, all fixtures were given the upgrade.
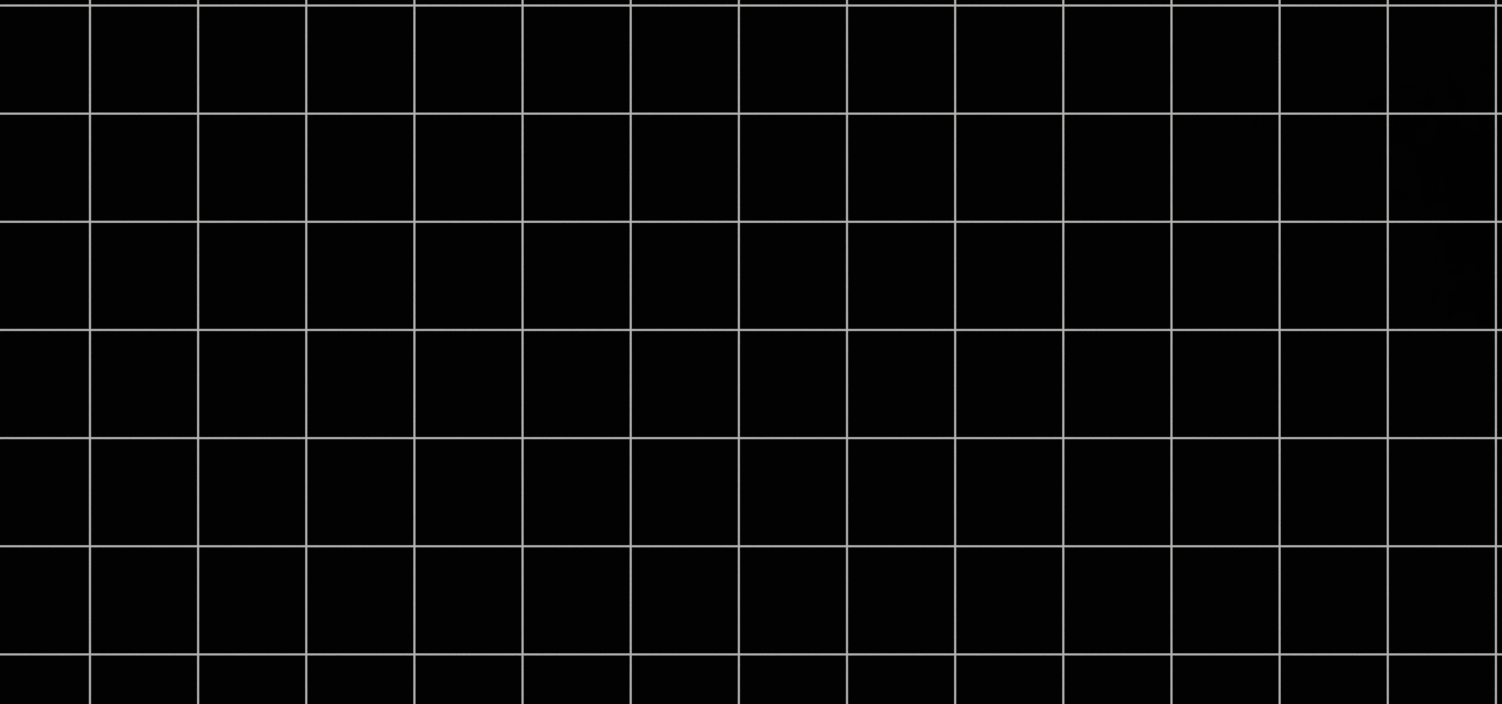
Nuclear Power Plant Open Phase Protection Cabinet Trade Show Demo-Showcase: Animation,3d Design & Engineering knowledge
Digital Cabinet Animation
Analog Cabinet Animation
During my first internship I was tasked with creating a 3d model of the open phase protection cabient’s. These cabinets were used on nuclear power plants. The purpose of the 3d model was to showcase the cabinet during trade shows, thus I also created animations of them. The animations seen to the left are the animations prior to rendering, hence the low quality.
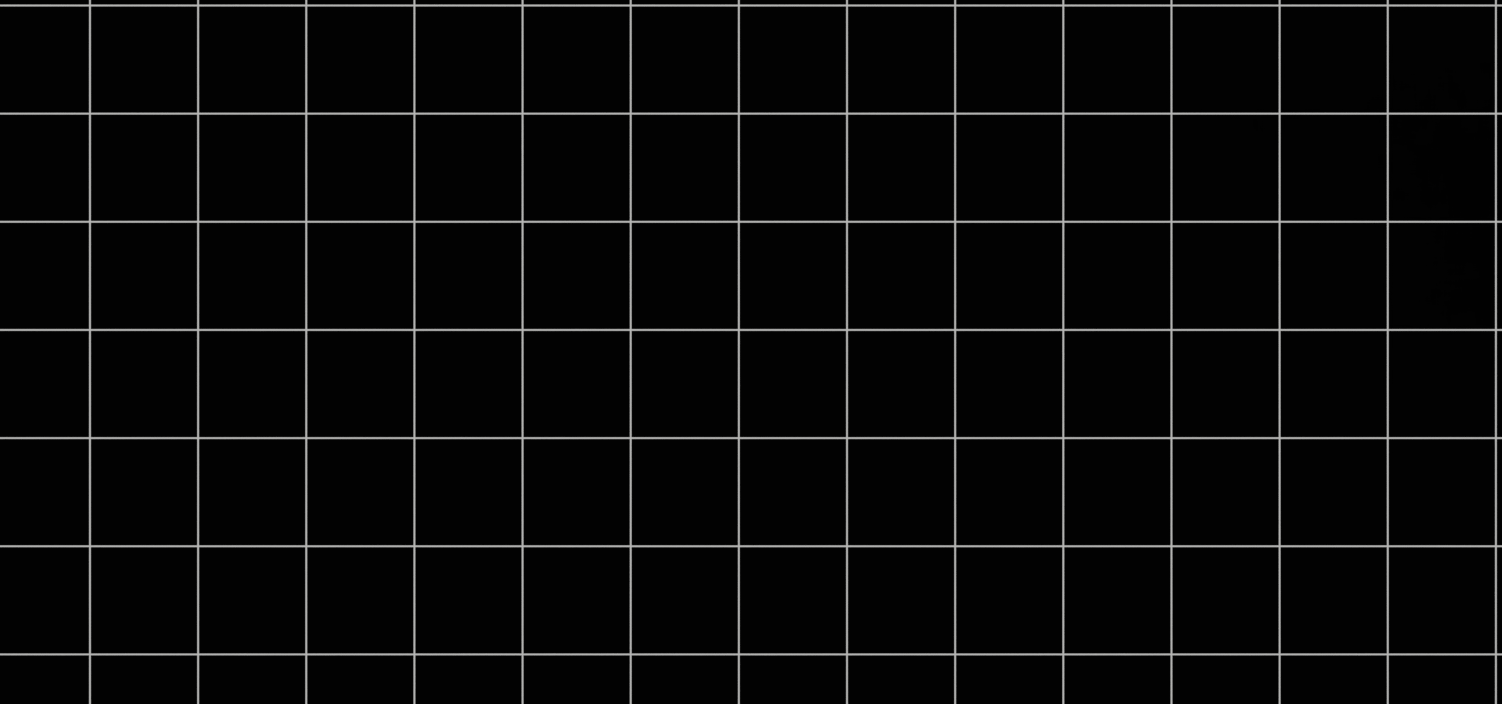
Layout Changeover and Saving Calculations-Showcase: Engineering knowledge , Layout Planning & computational finance
A Significant layout change was in order after cycle/TAK time and most study calculations showed we would not meet the demand of 500-700k F.G. Assembly’s. I proposed several layouts that utilized conveyors to greatly increase cycle time. The layouts also enabled better ergonomics and decreased operator steps. After the layout seen to the left was accepted I was charged with sourcing the conveyors which had to meet strict specifications due to the welded parts. Also to note, I had to calculate the proper conveyor speeds and feeds.